http://www.cworks.com.my/cw_download.asp
Es necesario el registro para poder descargar el programa, es la versión gratuita y esta en español favor de descargar e instalar
viernes, 15 de mayo de 2015
lunes, 11 de mayo de 2015
SISTEMAS DE BANDAS Y POLEAS
Desarrollo del diseño
Una banda es un elemento flexible capaz de transmitir potencia que sienta en forma
Ajustada sobre un conjunto de poleas o poleas acanaladas. Cuando se utiliza para reducir de velocidad, como en este caso, la polea acanalada más pequeña se monta en el eje de alta velocidad el cual estará acoplado a un motor eléctrico AC síncrono Torque normal, La polea de mayor ira acoplada a un eje central como se muestra en la siguiente ilustración. En este eje central trasmite la potencia, por medio de un conjunto de engranajes helicoidales y rectos, a otros dos ejes los cuales irán acoplados a un molino de bolas y a una mezcladora de cemento respectivamente.

Ilustración 1.Esquema de transmisión general.
Por medio del software Maximizer proporcionado por el fabricante de bandas de transmisión Goodyear, se obtendrá un diseño eficiente para esta aplicación; Los datos de entrada de la maquinaria y sus elementos mecánicos son los siguientes.

Ilustración 2. Parámetros operación maquinaria.
Cálculo de transmisión por banda
Se supone que la maquinaria, en este caso tanto la mezcladora de cemento, como el molino de bolas operaran los 6 días de la semana, por consiguiente se tiene que:

1.1 Cálculo de potencia en el motor.
Con los datos de operación de maquinaria y teniendo en cuenta las eficiencias de los componentes mecánicos presentes en los ejes, determinamos la potencia en el eje S1 o eje central.

Donde:

Por consiguiente la potencia del motor se determina de la siguiente manera.

1.2 Cálculo relación de transmisión por banda.
A continuación se procede a determinar la relación de transmisión por banda, de la siguiente manera.
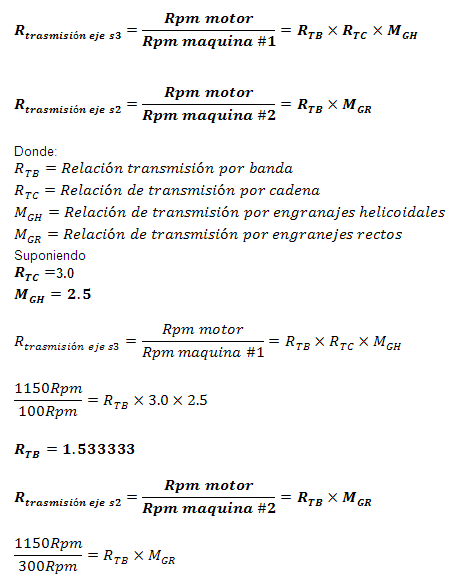
Remplazando el valor hallado anteriormente para la relación de transmisión por banda se obtiene el siguiente valor para la relación de transmisión por engranajes rectos.

Por consiguiente determinamos las Rpm de la polea inducida de la siguiente manera.

1.3 Cálculo del factor de servicio.
Este factor de servicio depende del tipo de maquinaría que se utiliza, para este caso tendremos una mezcladora de cemento y un molino de bolas, por consiguiente con ayuda de la tabla para factores de servicio del software maximizer tendremos los siguientes valores.
- Máquina # 1 (Molino de bolas).
Banda sincrónica=1.9
Banda V=1.4

Leer más: http://www.monografias.com/trabajos82/diseno-sistema-trasmision-polea-banda/diseno-sistema-trasmision-polea-banda.shtml#ixzz3Zr40HTpp
CIRCUITOS ELECTRICOS
1. Elementos de un circuito eléctrico
Se denomina circuito eléctrico al conjunto de elementos eléctricos conectados entre sí que permitengenerar,transportar y utilizar la energía eléctrica con la finalidad de transformarla en otro tipo de energía como, por ejemplo, energía calorífica (estufa), energía lumínica (bombilla) o energía mecánica (motor). Los elementos utilizados para conseguirlo son los siguientes:
- Generador. Parte del circuito donde se produce la electricidad, manteniendo una diferencia de tensiónentre sus extremos.
- Conductor. Hilo por donde circulan los electrones impulsados por el generador.
- Resistencias. Elementos del circuito que se oponen al paso de la corriente eléctrica .
- Interruptor. Elemento que permite abrir o cerrar el paso de la corriente eléctrica. Si el interruptor está abierto no circulan los electrones, y si está cerrado permite su paso.
2. Resistencias de los conductores eléctricos
La resistencia es la oposición que encuentra la corriente eléctrica para pasar por los materiales y esta depende de tres factores:
- El tipo de material. Cada material presenta una resistencia diferente y unas características propias, habiendo materiales más conductores que otros. A esta resistencia se le llama resistividad [ρ] y tiene un valor constante. Se mide [Ω·m].
- La longitud. Cuanto mayor es la longitud del conductor, más resistencia ofrece. Se mide en metros [m].
- La sección. Cuanto más grande es la sección, menos resistencia ofrece el conductor. Por lo tanto, presenta más resistencia un hilo conductor delgado que uno de grueso. Se mide en [m 2].
- La resistencia de un conductor se cuantifica en ohmios (Ω), y se puede calcular mediante fórmula:R = ρ • l / s
3. Interpretación del código de colores de una resistencia
Las resistencias comerciales (las que se acostumbran a usar para hacer prácticas de circuitos eléctricos) tienen 4 anillos pintados que sirven para identificar su valor.
El primer anillo corresponde a la primera cifra, el segundo anillo a la segunda cifra, el tercer anillo al número de ceros y el cuarto anillo al límite de tolerancia de la resistencia.
El código de colores de las resistencias es el siguiente:
Resistencia (Ω)
Color
|
1 a Cifra
|
2 a Cifra
|
3 a Cifra
|
4 a Cifra
|
ninguno
|
-
|
-
|
-
|
±20%
|
Plata
|
-
|
-
|
10 -2
|
±10%
|
Oro
|
-
|
-
|
10 -1
|
±5%
|
Negro
|
-
|
0
|
10 0
| |
Marrón
|
1
|
1
|
10 1
| |
Rojo
|
2
|
2
|
10 2
| |
Naranja
|
3
|
3
|
10 3
| |
Amarillo
|
4
|
4
|
10 4
| |
Verde
|
5
|
5
|
10 5
| |
Azul
|
6
|
6
|
10 6
| |
Lila
|
7
|
7
|
10 7
| |
Gris
|
8
|
8
|
10 8
| |
Blanco
|
9
|
9
|
10 9
|
4. Asociación de resistencias
Las resistencias (y otros elementos del circuito)pueden conectarse de dos formas diferentes:
- Asociación en serie. Los elementos asociados se colocan uno a continuación del otro. La corriente eléctrica tiene un único camino por recorrer, habiendo así la misma intensidad en todo el circuito.Por ejemplo, en caso de tener cuatro resistencias conectadas en serie, la resistencia equivalente se puede calcular como:R eq = R1 + R2 + R3 + R4
- Asociación en paralelo. Se crean derivaciones en el circuito. La corriente eléctrica que sale delgenerador tiene distintos caminos por recorrer.Por ejemplo, en caso de tener cuatro resistencias asociadas en paralelo, la resistencia equivalente del circuito se calcula como:1/R eq = 1/R1 + 1/R2 + 1/R3 + 1/R4
Para entender y poner en práctica, dispones de un juego interactivo sobre la asociación de resistencias.
Todos los componentes de un circuito eléctrico son representados graáficamente mediante símbolos elementalesaceptados por normas internacionales. Los esquemas de los circuitos eléctricos son dibujos simplificados que se utilizan para ver de forma clara y rápida como están conectados los circuitos.

6. La Ley de Ohm
Son varias las leyes que han estudiado los circuitos eléctricos. Entre ellas destaca la del año 1827 cuando, de forma experimental, Georg Simon Ohm encontró la relación que se podía expresar de forma matemática entre las tres magnitudes más importantes de un circuito eléctrico: diferencia de potencial, intensidad de corriente y resistencia.
La ley de Ohm es la ley fundamental de la corriente eléctrica que dice:
"En un circuito eléctrico, la intensidad de la corriente que lo recorres directamente proporcional a la tensión aplicada e inversamente proporcional a la resistencia que este presenta".
Y se expresa de la siguiente manera:
V=R • I
En el siguiente juego interactivo puedes entender de una manera más gráfica la ley de Ohm.
7. La Ley de Joule
Cuando por un conductor circula corriente eléctrica, este se calienta y produce calor. Esto es debido a que parte deltrabajo que se realiza para mover las cargas eléctricas entre dos puntos de un conductor se pierde en forma de calor.
El año 1845, James Prescott Joule fue capaz de encontrar la ley que permite calcular este efecto, viendo que este trabajo disipado en forma de calor es:
- Proporcional al tiempo durante el que pasa la corriente eléctrica.
- Proporcional al cuadrado de la intensidad que circula.
- Proporcional a la resistencia del conductor.
Se expresa de la siguiente manera:
W = R • I 2 • t
El efecto Joule limita la corriente eléctrica que pueden transportar los cables de las conducciones eléctricas. Este límite asegura que la temperatura que pueden conseguir los cables no pueda producir un incendio. Una manera de asegurar que no supere el límite es utilizando un fusible: un dispositivo formado por un hilo de metal que va conectado en serie al circuito general de la instalación eléctrica.
MOTOR TRIFASICO
Conexión de motores trifásicos a la red
Hasta ahora vimos como realizar una carga trifásica a partir de impedancias monofásicas. Sin embargo, hay receptores que son fabricados como cargas trifásicas y sus impedancias de fase no se pueden conectar por separado. Son sobretodo los motores y los transformadores trifásicos.
Los motores trifásicos presentan lógicamente tres devanados (tres impedancias) y seis bornes. Los fabricantes, para facilitar las conexiones (sobretodo el triángulo), disponen en la caja de bornes una colocación especial de estos. Observa la Fig y fíjate que las conexiones para realizar un triángulo son:
- X con V
- Y con W
- Z con U
En vista de esto, la caja de bornes viene distribuida como puedes ver , lo que ayuda mucho para conectar en triángulo pues este se realiza uniendo bornes en vertical, mediante conectores o chapas metálicas.

En la siguiente Fig. podemos ver la placa de características técnicas de un motor trifásico. Observa que la potencia, velocidad y frecuencia nominales son 15 (Kw), 2910 (rpm) y 50 (Hz) respectivamente. Pero ¿y la tensión y corriente nominales?


Estas magnitudes dependen de la conexión de los devanados del motor. Por un lado puedes ver que la tensión y corriente nominales son 400(V), 29 (A) en conexión estrella y 230 (V), 50 (A) en conexión triángulo. Los motores y las cargas trifásicas en general, son flexibles y pueden conectarse a redes con distinta tensión de línea, sin más que variar la conexión. En Fig. de la derecha puedes ver dibujadas ambas conexiones; observa que la tensión nominal de cada devanado es 230 (V), tanto en estrella como en triángulo y que este valor no se puede superar, sino el motor se sufrirá calentamientos excesivos.
En vista de estas características, si vamos a conectar este motor en una instalación de 400 V (de línea), debemos hacerlo en estrella y consumirá 29 (A) nominales de corriente de línea. Si posteriormente tenemos que trasladarlo a una instalación vieja de 230 V (de línea), el motor funcionará sin perder ninguna de sus prestaciones, pero debe conectarse en triángulo absorbiendo 50 (A) nominales de corriente de línea. Como en ambos casos se trata de un motor de 15 (Kw), bajo una red de menos tensión, consume más intensidad nominal (en triángulo). Normalmente en la mayoría de placas de características, la tensión y corriente nominales vienen indicadas de la siguiente forma:

Como regla general debes recordar que:
1.- La tensión mayor y la corriente menor corresponden a la conexión estrella.
2.-La tensión menor y la corriente mayor corresponden a la conexión triángulo.
3.-La relación entre las dos tensiones y entre las dos corrientes es
:
2.-La tensión menor y la corriente mayor corresponden a la conexión triángulo.
3.-La relación entre las dos tensiones y entre las dos corrientes es


!!! Cualquier carga trifásica puede conectarse a dos tensiones red, sin más que variar su conexión (estrella o triángulo). Esta característica se puede ver sobretodo en las placas de los motores trifásicos, donde se especifican dos tensiones y dos corrientes nominales!!!
RECTIFICADORAS
MAQUINAS PARA EL ACABADO DE SUPERFICIES
La definición de grado de acabado superficial, independiente del sistema con que se haya obtenido, implica la introducción de parámetros relacionados con la microgeometría de las superficies.
El acabado superficial carece de interés como problema en sí mismo; pero afecta directamente, por su grado más o menos notable, a las condiciones de rozamiento, desgaste, formación de arrugas, lubricación, etc. en órganos móviles y, en general, es un factor ligado a la precisión de las dimensiones en la construcción de elementos mecánicos. En consecuencia, las máquinas acabadoras (rectificadoras, super cavadoras, pulidoras y lapeadoras) son muy cuidadas, rígidas y bien equilibradas dinámicamente.
RECTIFICADORAS
El rectificado es una operación que se efectúa en general con piezas ya trabajadas anteriormente por otras máquinas herramientas hasta dejar un pequeño exceso de metal respecto a la dimensión definitiva. El rectificado tiene por objeto alcanzar en las dimensiones tolerancias muy estrictas y una elevada calidad de acabado superficial; se hace indispensable en el trabajo de los materiales duros o de las superficies endurecidas por tratamientos térmicos. Las herramientas empleadas son muelas giratorias.
MUELAS
Están compuestas por granos abrasivos aglomerados en dispersión en un cemento que define la forma de la herramienta. Los granos representan infinitos filos que, al actuar con elevada velocidad sobre la pieza en elaboración, arrancan minúsculas partículas de material. Este modo de trabajar indica también los requisitos que deben poseer los abrasivos: dureza, resistencia al desgaste y resistencia a la rotura.
Los abrasivos utilizados actualmente son artificiales. El Alundum (hasta 99 % de Ah03 cristalizado) conocido en el comercio también con los nombres de Corundum, Coralund, Aloxite y Alucoromax, se utiliza generalmente para trabajar aceros. El carburo de silicio (SiC) conocido como Carborundo. Crystolon y Carborite, más duro, pero menos resistentes a la rotura, se utiliza para materiales durísimos que son poco tenaces (fundiciones y carburos metálicos) o materiales blandos (aluminio, latón y bronce). El Borolón es el abrasivo artificial más duro y resistente que se conoce.
La dimensión de los granos está vinculada a la utilización de la muela: para muelas desbastadoras se emplea grano grueso; para operaciones de rectificado se pasa de los granos medianos a los finos, hasta llegar a los polvos utilizados para el pulido. El número índice del grosor de los granos expresa el número de hilos por pulgada contenido en el último cedazo separador atravesado (los granos más finos llegan hasta 240 hilos).
Los aglomerantes de las muelas pueden ser cerámicos, de silicato sódico y arcilla, o elásticos.
Los aglomerantes cerámicos, constituidos por arcillas, cuarzo y feldespato, que reducidos a polvo se empastan con el abrasivo y se conforman con moldes apropiados, después de un periodo de desecación lenta se vitrifican en hornos de túnel (a unos 1.500 0C durante 3-5 días). Son de uso corriente y poseen óptimas cualidades, pero presentan poca elasticidad. Los aglomerantes de silicato sódico y arcilla requieren una cocción a 200-300 0C; con esta pasta se construyen muelas menos duras que las anteriores y con acción abrasiva reducida; son más económicas, pero de menor duración. Los aglomerantes elásticos, adoptados para la construcción de muelas delgadas para corte o capaces de un elevado grado de acabado, pueden ser el caucho vulcanizado, la baquelita u otras resinas sintéticas, o goma laca.
Los datos característicos de una muela son el tipo de abrasivo, su granulación (gruesa, mediana, fina o muy fina), su tenacidad (muy blanda, blanda, mediana, dura o muy dura), su estructura (cerrada,, mediana o abierta) y el tipo de cemento aglomerante.
RECTIFICADORAS PARA SUPERFICIES CILÍNDRICAS EXTERIORES
Estas máquinas herramientas efectúan el trabajo a que están destinadas realizando el esquema de movimientos que se describe a continuación.
El movimiento de corte consiste en una rápida rotación de la muela en torno a su eje, con un sentido tal que la velocidad periférica en la zona de contacto con la pieza se dirija hacia abajo. Esta velocidad debe ser la máxima posible en compatibilidad con la resistencia de la muela, cuyo aglomerado está solicitado por fuerzas centrífugas. Para el rectificado de cilindros exteriores de acero con muelas de aglomerado cerámico pueden alcanzarse velocidades periféricas de 20-30 m/s.
El movimiento de avance periférico pertenece a la pieza y consiste en una rotación en torno a su propio eje. Su sentido tiene que producir una velocidad relativa entre la pieza y la muela igual a la suma de ambas velocidades y simultáneamente debe impedir una acción de arrastre sobre la pieza. Sirve para alimentar, en una sección transversal dada, nuevo material para arrancar y, por tanto, su velocidad depende del propio material, de la profundidad de la pasada y de la longitud del arco de contacto entre la pieza y la muela. Para los aceros es de 8-15 m/mn y llega a 40 m/mn para las aleaciones ligeras.
El movimiento de avance axial es una traslación axial de la pieza para la alimentación longitudinal. Su entidad (expresada en mm/vuelta de la pieza) depende del material en elaboración, de las dimensiones de la pieza, del grado de acabado deseado y, en todo caso, no debe superar el valor de la anchura de la muela.
El movimiento de regulación radial es intermitente; se comunica a la muela al final de cada pasada completa y la desplaza una longitud igual a la profundidad de la pasada. En el rectificado exterior para el desbastado de los aceros, las pasadas suelen ser de 0,02-0,06 mm y para el acabado, de 0,005-0,02 mm.
La máquina está constituida por una bancada que actúa como armadura y tiene en su parte superior las guías horizontales longitudinales sobre las que está montada la mesa portapiezas y las cortas guías transversales, perpendiculares a las anteriores, necesarias para la regulación gradual de las posiciones del cabezal portamuelas. En la bancada están contenidos el motor y los mecanismos del movimiento de avance de la mesa, en el caso de accionamiento mecánico obtenido con piñón y cremallera, o la bomba y los circuitos cuando el accionamiento es con cilindros hidráulicos. Contiene también el circuito de refrigeración, constituido por un gran depósito de decantación, una electrobomba y un filtro o separador magnético de las limaduras.
El cabezal portamuelas incluye el motor eléctrico (3-5 CV) del movimiento de corte, que pone en rotación el husillo portamuelas con una transmisión de correas trapeciales. El árbol del husillo, generalmente rotatorio con velocidad única, está montado sobre cojinetes de juego regulable y con lubricación especialmente cuidada por la gran precisión requerida por el rectificado. La muela, por su fragilidad, está montada sobre el árbol entre platinas de gran diámetro y con discos clásicos interpuestos. Los movimientos del cabezal portamuelas son trasversales y pueden ser manuales (obtenidos con tornillos micrométricos), automáticos continuos, o bien intermitentes al final de cada carrera o presentando periódicamente a la pieza un calibre de control tarado previamente.
El cabezal porta piezas está montado sobre unas pequeñas guías practicadas en la mesa y se fija sobre ésta en la posición impuesta por las dimensiones de la pieza. Contiene los mandos del movimiento de avance periférico, es decir, el motor (0,5 CV) y el cambio de velocidades, que puede ser hidráulico o mecánico de conos de poleas. Para trabajos entre puntas se dispone de un contracabezal, fijado sobre guías a la mesa y dotado de una contrapunta y también, generalmente, de un dispositivo avivador del grano de las muelas.
El esquema de los movimientos se modifica en las rectificadoras para piezas de grandes dimensiones, en las cuales el movimiento de avance axial lo efectúa el grupo portamuelas.
RECTIFICADORES PARA INTERIORES
Estas máquinas realizan los mismos movimientos relativos entre pieza y herramienta que las ya citadas para exteriores y adoptan soluciones cinemáticas y de accionamiento análogos, pero con complicaciones derivadas de la clase especial del trabajo. El hecho de tener que trabajar superficies interiores impone límites a las dimensiones de la muela que, por tanto, para trabajar con velocidades de corte económicas debe poseer velocidades angulares muy altas (de 20.000-100.000 rpm) y necesita frecuentes avivados del grano. Esto implica la existencia de un dispositivo mecánico para la recuperación del error producido.
Como se ha indicado, el movimiento de trabajo se asigna a la muela, lo mismo que el movimiento de regulación radial; mientras que el movimiento de avance periférico lo realiza la pieza.
Los dos tipos principales de rectificadores para interiores se clasifican partiendo de la forma del movimiento de avance axial. En el tipo de avance axial de la pieza, adaptado al trabajo de piezas de dimensiones no excesivas, la pieza, bloqueada en el árbol del cabezal por un autocentrador, se desplaza con la mesa que se desliza por unas guías longitudinales situadas en la parte izquierda de la bancada. Entre el cabezal y la mesa se halla un disco orientable para la rectificación de orificios cónicos. A la derecha de la bancada existen unas guías transversales para el cabezal portamuelas.
En el tipo de avance axial de la muela, el movimiento de avance longitudinal se asigna al cabezal portamuelas. Este, montado sobre una mesa deslizable sobre las guías de la bancada, puede realizar desplazamientos hasta de 400-500 mm con velocidades regulables de manera continua.
Para el rectificado de orificios en piezas asimétricas y de grandes dimensiones existe una tercera solución en cuyo esquema cinemático se asigna a la muela, aparte del movimiento de trabajo, uno planetario en torno al eje de la superficie por rectificar; las regulaciones radiales se efectúan variando el intereje entre la muela y el orificio. Según los tipos, el movimiento axial de avance puede asignarse a la muela directa o a la pieza.
RECTIFICADO, LABRADO ABRASIVO Y ACABADO
El trabajo con esmeril es un proceso en el que se desprenden virutas o rebabas mediante aplicación de aristas afiladas muy pequeñas de partículas duras, que suelen ser de material sintético. En muchos casos partículas abrasivas (esmeril) están aglomeradas forma do ruedas de diferentes formas y tamaños.
En aquellas ocasiones en que estas ruedas, llamadas muelas, se utilizan para producir dimensiones exacta superficies lisas, el proceso de esmerilado se denomina rectificado.
Cuando el objetivo principal es la eliminación rápida de metal para obtener una forma deseada o dimensiones aproximadas, el proceso se denomina labrado abrasivo.
Si las finas partículas abrasivas se utilizan para producir superficies muy lisas y mejorar la estructura metalúrgica de la superficie para una mejor apariencia, proceso se denomina acabado.
ABRASIVOS SINTÉTICOS
• El óxido de aluminio (A1203) funciona mejor en los aceros al carbono y de aleación, hierro maleable recocido, bronce duro y metales similares. Las muelas de A1203 no se utilizan en el esmerilado de materiales muy duros, como el carburo de tungsteno, debido a que los granos se desafilan antes de la ruptura. Algunos de los nombres comerciales comunes del óxido de aluminio son Alundum y Aloxita.
• Los cristales de carburo de silicio (SiC) son muy duros. De acuerdo con la escala Moh, poseen un índice de 9.5; el diamante tiene una dureza de 10 en dicha escala. Los cristales de SiC son frágiles, lo que limita su utilización. Las muelas de carburo de silicio se recomiendan para materiales de baja resistencia a la tensión, como hierro colado, latón, piedra, caucho (o hule), cuero y carburos cementados.
• El nitruro de boro cúbico (CBN) es la segunda sustancia más dura natural o artificial. Es útil para esmerilar herramientas y troqueles de aceros de gran dureza y tenacidad.
• Los diamantes pueden clasificarse como naturales y sintéticos. Los diamantes comerciales se fabrican actualmente como de alta, media y baja resistencia al impacto.
TAMAÑO DEL GRANO
Para obtener una acción uniforme de corte, los granos abrasivos están graduados en varios tamaños, indicados por los números de 4 al 600. El número indica la cantidad de aberturas por pulgadas lineales en una criba estándar, a través de la que pasaría la mayor parte de ¡as partículas de un tamaño específico.
Los granos cuyos tamaños van del 4 al 24 se llaman “gruesos”; los de 30 a 60 se denominan “medianos”, y los que van del 70 al 600 se conocen como “finos”.
Los granos finos producen superficies más lisas que los gruesos, pero no pueden eliminar tanto metal como éstos.
Los materiales aglomerantes tienen los siguientes efectos en el proceso esmerilado:
1. Determinan la resistencia y la velocidad máximas de la muela.
2. Determinan si la rueda debe ser rígida o flexible.
Establecen la fuerza disponible para retener las partículas. Si para desprender los granos se requiere sólo una pequeña fuerza, se dice que la muela es suave. Para los materiales suaves se utilizan muelas duras, y para los materiales duros, muelas suaves. Los materiales aglomerantes que se utilizan son los de vitrificado, silicato, caucho o hule, resinoides, lacas y de oxicloruro.
ESTRUCTURA O ESPACIAMIENTO DE LOS GRANOS
La estructura se relaciona con el espaciamiento de los granos abrasivos. Los materiales dúctiles y suaves requieren un mayor espaciamiento para acomodar las virutas relativamente grandes. Un acabado fino requiere una muela con poco espaciamiento intergranular.
VELOCIDADES
La velocidad de las ruedas depende de su tipo, del material aglomerante y de las condiciones de operación. Las velocidades de las ruedas varían entre 4500 y 18000 pie/min (entre 1 400 y 5 500 m/min). Las velocidades de trabajo dependen del tipo de material, de la operación de esmerilado y de la rigidez de la máquina. Las velocidades de trabajo varían entre 15 y 200 pie/min.
AVANCES
El avance transversal depende del ancho de la muela o rueda de amolar. Para un esmerilado de desbaste este avance varía de un medio a tres cuartos del ancho de la rueda. Para el acabado se requiere un avance más pequeño, que varía entre un décimo y un tercio del ancho de la muela.
PROFUNDIDAD DE CORTE
Las condiciones de esmerilado de desbaste determinan la máxima profundidad de corte. En la operación de acabado la profundidad de corte suele ser pequeña, de 0.0005 a 0.001 pulg (de 0.013 a 0.025 mm). Es posible lograr buen acabado superficial y poca tolerancia mediante el “chisporroteo” o dejando que la rueda se desplace sobre la pieza de trabajo sin aumentar la profundidad de corte, hasta que se apagan o extinguen las chispas. La relación de esmerilado, o número G, es el cociente de las pulgadas cúbicas de material para labrar eliminadas, y las pulgadas cúbicas que pierde la rueda de esmeril. La relación G es importante para calcular los costos del labrado abrasivo y del esmerilado, que puede calcularse con la siguiente expresión:
C = Ca + L
G tq
en donde,
C = costo específico de eliminar una pulgada cúbica del material
Ca= costo del abrasivo, $/pulg3
G = relación del esmerilado
L = gastos generales y por mano de obra, $ / h
q = rapidez de labrado, pulg3/h
t = tiempo que la rueda está en contacto 1 con la pieza de trabajo
Entre las máquinas de rectificado y labrado abrasivo se encuentran las siguientes:
Rectificadoras superficiales: de mesa oscilante o giratoria.
Rectificadoras cilíndricas, para trabajo entre centros, sin centro, cigüeñal para conformado de roscas y engranes y para trabajo interno y en otras aplicaciones.
Rectificadora de plantilla.
Rectificadoras para herramienta y cortadores.
Debastadoras para trabajos en piezas de fundición.
6. Recortadoras y perfiladoras.
7. Para labrado abrasivo, de banda, disco y material suelto.
8. Para trabajo continuo, intermitente y vibratorio.
ACABADO SUPERFICIAL
Este proceso produce un terminado superficial extrafino; además, se eliminan las marcas de la herramienta y se alcanzan tolerancias muy estrechas. A continuación se analizan con brevedad algunos de estos procesos.
PULIDO BASTO
Es un proceso abrasivo a poca velocidad. En él se utilizan piedras de grano fino abrasivas para eliminar cantidades muy pequeñas de metal, que por lo general dejan otros procesos de esmerilado. La cantidad de metal que se elimina suele ser inferior a 0.005 pulg (0.13 mm). Debido a las bajas velocidades se reducen el calor y la presión, obteniéndose un excelente control metalúrgico y de tamaño.
PULIDO FINO (O PULIMENTADO)
Es un proceso abrasivo de acabado superficial en el que partículas finas de abrasivo se introducen en un material como grasa, aceite o agua, y se embeben en un material blando, denominado pulimentador. Los pulimentadores metálicos deben ser mucho más suaves que el material de trabajo, y suelen estar hechos de hierro colado gris de grano pequeño. Cuando el hierro fundido no es adecuado, se utilizan otros materiales, como acero, cobre y madera.
Puesto que el pulimentador cargado se frota contra una superficie, se eliminan pequeñas cantidades de material de la superficie más dura. La cantidad de material eliminado suele ser menos que 0.001 pulg (0.03 mm).
SUPERACABADO
Es un proceso para mejorar las superficies en el que se eliminan fragmentos indeseables, dejando una base de metal sólido cristalino. Como en el pulido basto, también se utilizan piedras abrasivas finas, pero el tipo de movimiento es diferente.
En este proceso se utilizan recorridos cortos muy rápidos, muy poca presión de acabado y no de dimensionado, y es posible suponerlo a otras operaciones de terminado.
LABRADO ULTRASÓNICO
En el labrado ultrasónico, el material se elimina de la pieza de trabajo mediante la proyección a muy alta velocidad de partículas abrasivas en una pasta aguada y por medio de la acción de un transductor ultrasónico.
LUSTRADO
Las ruedas lustradoras se hacen de diversos materiales muy suaves. Aunque el más utilizado es la muselina, para aplicaciones especiales también se utiliza franela, lino, henequén y papel grueso. Este proceso suele dividirse en dos operaciones: emparejado y abrillantado. La primera se utiliza para pulir la superficie y la segunda para producir el lustre intenso. Los abrasivos que se utilizan son polvos extremadamente finos de óxido de aluminio, trípoli (un silicio amorfo), pedernal o cuarzo, carburo de silicio y óxido rojo de hierro. Las velocidades para el lustrado varían de 6 000 a 12 000 pie / minuto.
En el electro pulido se trabaja inversamente respecto a la galvanostegia; es decir, aquí la pieza de trabajo es el ánodo y no el cátodo, y se elimina material.
RECTIFICADORA UNIVERSAL DE HERRAMIENTAS Y FRESAS
- Una máquina de múltiples aplicaciones capaz de afilar una gama muy amplia de herramientas en acero rápido, herramientas con punta de carburo, cortador rotatorio de metales fresa espiral, sierra para ranurar metales, cortadoras cilíndricas, fresa de disco y de refrentar, cortadora involuta de engranajes, cortadora de hierros angulares, cortadora convexo y cóncavo, fresa de espiga, cortadora de ranuras, etc.
- Apropiado también para rectificar ángulos de escariadores y cortar el frente por las estrías de machos
- Con accesorios opcionales especiales se puede rectificar broca de barrena, machos y rectificar en radio
- Velocidad del husillo: 2800 rpm y esta controlado por un conmutador inversor
- Cabezal sobre una placa de base grabado que gira por 360o y puede estar engrapado en cualquier posición
- La columna de hierro fundido puede estar ajustado verticalmente y engrapado en cualquier posición. El movimiento esta controlado precisamente por medio de un micrómetro
- Mesa superior de trabajar tiene una ranura para fijar portaherramienta, etc. y también para localización precisa de centros sueltos. Esta graduado en ambos direcciones del Cero y gira por 180o
- Travesero transverso controlado precisamente por rueda de mano fijado con micrómetro
RECTIFICADORA DE PEDESTAL
- Apropiado para trabajo de servicio pesado en Industria de forjadura, taller de fundición, etc.
- Todas maquinas equipadas con batea y sistema de enfriamiento
- Velocidad de carga (rpm) es de 3000.
ESMERILADORA DE SUPERFICIE
- Avance longitudinal, hidráulico automático
- Avance transversal con sistema de trinquete mecánico
- Movimiento vertical por mano con avance y rápido para avance fino
- Velocidades del eje (RPM): 2800
ESMERILADORAS CILÍNDRICAS HIDRÁULICAS
- Carrera Manual Longitudinal de la mesa por Cremallera y Piñón / Carrera Automática por Mecanismo Hidráulico
- Cabezal Portapiedra con Movimiento Hidráulico Rápido
AMOLADORA SIN PUNTAS
- Ambos cabezales portapiedras viene con rectificador hidráulico de ruedas abrasivas con control de velocidades variables
- Fuente de energía hidráulica independiente detrás de la maquina
CONCLUSIONES
- Las maquinas herramientas se utiliza para dar forma o modelar materiales sólidos, especialmente metales
- Cada máquina posee sus órganos propios de producción y transmisión del movimiento.
- El rectificado es una operación que se efectúa en general con piezas ya trabajadas anteriormente por otras máquinas herramientas hasta dejar un pequeño exceso de metal respecto a la dimensión definitiva.
RECOMENDACIONES
Enseñsarle a los estudiantes mas acerca del uso de estas máquinas herramientas, ya que son muy importantes a través de nuestra carrera a la hora de desempeñar un trabajo en esta área.
Facilitar más material sobre este tema a centros de estudios ya que están muy escasos de libros.
Crear un taller más amplio con todas las máquinas herramientas y mantenerlas en buen estado.
Suscribirse a:
Entradas (Atom)